Room for Improvement in Workplace Safety
“Safety first!” If you work in the manufacturing sector, you’ve probably seen and heard that phrase a million times. And there’s nothing wrong with that. No one wants to work in a facility that puts them at risk of serious injury or even death.
Unfortunately, too many workers do suffer workplace injuries every year. The number and severity of these injuries remain a constant reminder that there’s always room for improvement when it comes to workplace safety.
In a recent EHS Today article, author Adrienne Selko notes that “US businesses need to ‘do significantly better’ in supporting workplace safety, according to a recent survey from BSI.” BSI’s Xavier Alcaraz notes that “[w]e’ve normalized a culture where…’safety first’ is promoted but supervisors look the other way when deadlines are at risk.”
Things don’t have to stay that way, however. Workers deserve better. BSI offers some practical advice for manufacturers seeking to improve workplace safety:
- “Safety culture: Foster an environment where safety is a systems-driven core value, encouraging reporting of potential hazards and near-misses without fear of reprisal. This contributes to both physical safety as well as psychological safety.”
- “Adopt a management systems approach for health and safety that emphasizes continuous improvement.”
- “Align safety goals with business goals.”
- “Safety training: Provide comprehensive safety training, including proper use of equipment, emergency procedures, and hazard recognition.”
That last suggestion is an important one that too many companies ignore. Of course, not all companies prioritize safety like they should, but even those wanting to improve don’t always know how to go about adequately training workers.
For companies looking to improve their safety training, partnering with established companies to provide industrial-quality training systems that will stand the test of time will help ensure the continued safety of the workforce.
For example, DAC Worldwide offers two safety training systems specifically designed to give employees the hands-on experience they need to master lock-out/tag-out skills:
- DAC Worldwide Lock-Out/Tag-Out Training System
- DAC Worldwide Electrical Lock-Out/Tag-Out Training System
Be sure to check out these training systems and contact a DAC Worldwide representative to learn how you can improve your training today!
- Published in News
Electrical Safety is no Joke
Did you hear the latest parental advice on how to keep kids from chewing on electrical cords? You ground them until they conduct themselves properly!
OK, we may have started this article with a (terrible, absolutely awful) joke, but we did so to make a point: electrical safety is no joke, especially in the workplace. In fact, bad dad jokes are the only time electrical safety is a laughing matter.
That’s a lesson that a plastic and resin manufacturer with facilities in Georgia and Alabama learned the hard way recently. According to a recent Plant Services article by Alexis Gajewski, “[a]n [Occupational Safety and Health Administration] OSHA investigation has determined that Crown USA Inc. could have prevented the death of a 37-year-old maintenance technician…if they were following required safety rules designed to keep machines from starting up during maintenance.”
Gajewski notes that “[t]he worker was inside an unlocked hooding palletizer, servicing the machine, when they suffered fatal crushing injuries.” OSHA Area Director Jeffery Stawowy said, “Employers must understand federal workplace safety regulations exist to help prevent tragedies like the one that occurred at Crown USA Inc.”
The resulting OSHA investigation revealed “eight serious and six other-than-serious violations. These violations include failing to implement adequate machine guarding, a lack of training on energy control procedures, exposing workers to serious respiratory hazards, and failing to provide proper personal protective equipment (PPE).”
Not only did a maintenance worker needlessly lose their life, but the company also “faces $98,699 in penalties.” Other companies would be wise to learn from Crown USA Inc.’s shortcomings and institute rigorous safety training, including adequate training on energy control procedures.
Manufacturers can always benefit from a regular audit of safety training. The best way to improve a workplace’s safety culture and teach workers to prioritize safety is to implement a quality safety program that teachers workers the knowledge and skills they need to stay safe in the workplace.
As previously mentioned, one of the most basic—and important—areas to focus on is the control of hazardous energy, often known by its more popular moniker “lock-out/tag-out or LOTO.” According to OSHA, “[e]nergy sources including electrical, mechanical, hydraulic, pneumatic, chemical, thermal, or other sources in machines and equipment can be hazardous to workers. During the servicing and maintenance of machines and equipment, the unexpected startup or release of stored energy can result in serious injury or death to workers.”
That’s exactly the lesson that Crown USA Inc. learned too late. Fortunately, “[p]roper lock-out/tag-out practices and procedures safeguard workers from hazardous energy releases.” Teaching workers hands-on LOTO skills will help them to understand how to properly control hazardous energy and maintain a safe work environment.
For companies looking to improve their safety training, partnering with established companies to provide industrial-quality training systems that will stand the test of time will help ensure the continued safety of the workforce.
For example, DAC Worldwide offers a safety training system specifically designed to give employees the hands-on experience they need to master lock-out/tag-out skills. Be sure to check out DAC Worldwide’s Lock-Out/Tag-Out Training System and contact a DAC Worldwide representative to learn how you can improve your training today!
- Published in News
Electrical Safety Training Sets the Stage for a Secure Workplace
My neighbor asked me to install a new electrical outlet in his master bathroom. He was eventually shocked to learn that I’m not a licensed electrician! OK, that’s an old—and terrible—joke, but it does underscore the importance of safety when it comes to working with electrical current.
In the modern industrial workplace, there are a whole host of skills that workers need to know. No matter how highly skilled a worker might be, however, nothing will matter if the fundamental basics of safety aren’t mastered.
When it comes to safety, one of the most important skills that workers must learn is how to work safely with electricity. According to a FacilitiesNet article by Ashley Beebe, “[w]hen working with electrical distribution systems and components, frontline maintenance technicians and engineers often face the potential for serious injury or death from electrocution or arc flashes, but knowledge of safety tips, procedures, codes and regulations can help technicians and engineers lessen the risk and potential for serious injury or death.”
That’s why, “[a]ccording to the Occupational Safety and Health Administration (OSHA), employees must not work near an electric current, any equipment, or a part they may come in contact with while on the job, unless it has been de-energized. If an electric current has not been de-energized, employees must be protected by isolation, insulation, warning signs or other methods.”
In safety training, the control of hazardous energy is often known by its more popular moniker “lock-out/tag-out or LOTO.” According to OSHA, “[p]roper lock-out/tag-out practices and procedures safeguard workers from hazardous energy releases.” Teaching workers hands-on LOTO skills will help them to understand how to properly control hazardous energy and maintain a safe work environment.
For companies looking to improve their safety training, a thorough review of current training materials is a great place to start. Do employees have access to hands-on training with actual components they’ll encounter on the job? If not, partnering with established companies to provide industrial-quality training systems that will stand the test of time will help ensure the continued safety of the workforce.
For example, DAC Worldwide offers a safety training system specifically designed to give employees the hands-on experience they need to master lock-out/tag-out skills. Be sure to check out DAC Worldwide’s Lock-Out/Tag-Out Training System and contact a DAC Worldwide representative to learn how you can improve your training today!
- Published in News
Safety Leaders Reveal Most Significant Challenges in the Workplace
What would you consider to be the most foundational skillset in the industrial workplace? If you did not answer “safety,” there are safety leaders everywhere who would like a word with you. In fact, you may be part of the problem!
Safety leaders are tasked with making sure the industrial workplace is as safe as possible for workers. There’s no greater threat to industrial efficiency and productivity than workplace accidents that injure workers and cause costly delays and downtime.
As more and more advanced automation technologies enter the workplace, safety leaders constantly face new challenges to keep workers safe as they work alongside new machinery. But safety shouldn’t just be the concern of a few leaders. All employees need to make safety a top priority.
According to a recent EHS Today article by Dave Blanchard and Nicole Stempak, “EHS Today’s National Safety and Salary Survey 2023 invited respondents (all of them EHS professionals) to share comments regarding their job situation, the safety profession, and the biggest professional challenges that they face.” Here are some of the top challenges identified by the nation’s safety leaders:
- Finding qualified employees
- The transition from a human-based workforce to a technology-based workforce
- Safety buy-in from the younger workforce
- Senior leadership buy-in
- Mental well-being
- Too many rules and regulations
- Profit over safety
- Training and job knowledge
- Employee turnover
- Older supervisors are retiring faster than we can train replacements to take their place
- Employee complacency
- Doing too much too fast
- Finding employees with the proper skillsets
- Keeping the workforce actively engaged in their own safety
As you can see, safety leaders face a wide variety of challenges in the modern industrial workplace. What can be done to improve a workplace’s safety culture? How can leaders influence others to prioritize safety, leading to fewer accidents? One solution is to implement a quality safety program that teachers workers the knowledge and skills they need to stay safe in the workplace.
One of the most basic—and important—areas to focus on is the control of hazardous energy, often known by its more popular moniker “lock-out/tag-out or LOTO.” According to the United States Department of Labor’s Occupational Safety and Health Administration (OSHA), “[e]nergy sources including electrical, mechanical, hydraulic, pneumatic, chemical, thermal, or other sources in machines and equipment can be hazardous to workers. During the servicing and maintenance of machines and equipment, the unexpected startup or release of stored energy can result in serious injury or death to workers.”
“Workers servicing or maintaining machines or equipment may be seriously injured or killed if hazardous energy is not properly controlled…Injuries may include electrocution, burns, crushing, cutting, lacerating, amputating, or fracturing body parts… Craft workers, electricians, machine operators, and laborers are among the millions of workers who service equipment routinely and face the greatest risk of injury.”
Fortunately, “[p]roper lock-out/tag-out practices and procedures safeguard workers from hazardous energy releases.” Teaching workers hands-on LOTO skills will help them to understand how to properly control hazardous energy and maintain a safe work environment.
For companies looking to improve their safety training, a thorough review of current training materials is a great place to start. Do employees have access to hands-on training with actual components they’ll encounter on the job? If not, partnering with established companies to provide industrial-quality training systems that will stand the test of time will help ensure the continued safety of the workforce.
For example, DAC Worldwide offers a safety training system specifically designed to give employees the hands-on experience they need to master lock-out/tag-out skills. Be sure to check out DAC Worldwide’s Lock-Out/Tag-Out Training System and contact a DAC Worldwide representative to learn how you can improve your training today!
- Published in News
Recognizing Red Flags: Training Workers to Prioritize Safety
Do you keep an eye out for red flags? If you’re still looking for that someone special, you might see red flags when their online dating profile indicates they’re unemployed and still living in their parents’ basement.
But those aren’t the red flags we’re talking about in this article. Red flags signify danger. They’re warning signs, and today’s workers need to recognize them in the workplace. Why? Their safety and wellbeing depends upon it.
Workplace safety remains a critical component of any industry’s success, yet it too frequently doesn’t get the attention it deserves. New technologies and the latest and greatest advances tend to capture the most attention, but the basics of safety can bring everything to a grinding halt if they’re ignored.
In this article, we’ll take a look at five red flags that workers must learn to recognize in order to make safety a top priority. We’ll also explain the importance of safety training and how the training tools offered by DAC Worldwide can help workers learn the skills that will keep them safe in the modern workplace.
5 Safety Red Flags Employees Must Learn to Recognize
How important is worker safety in your workplace? According to an IndustryWeek article by Matt Thiel and Dan Idzikowski, “nearly all [manufacturers] will say [safety is] a top priority…At the same time, the features and processes intended to keep people safe are rarely put to the test until a crisis occurs. It’s only when safety fails — when there is an injury or a near-miss — that companies question whether they are doing enough to protect workers.”
Modern industrial workplaces feature a wide variety of safety features designed to keep workers safe. Yet, workplace injuries remain a serious problem. For example, “more than 420,000 manufacturing workers were injured on the job in 2019, according to the U.S. Bureau of Labor Statistics, accounting for 15% of all nonfatal injuries in the private sector that year.”
What can be done to improve workplace safety? According to Thiel and Idzikowski, “[s]afety planning starts by imagining the unimaginable…it’s critical to play devil’s advocate and ask what could happen that shouldn’t, and how both the equipment and the operator will respond if it does.”
Once safety risks are identified, workers must be trained to recognize situations in which particular care must be taken to avoid injury. Otherwise, “[w]hen safety is treated as an afterthought, it’s only a matter of time until a preventable accident happens.” Here are five specific red flags Thiel and Idzikowski belive workers must learn to recognize:
- Access: Workers must learn to recognize situations in which “[o]perators can access hazardous areas while the hazard is present. Systems that require hands-on operator involvement…have built-in risks…Making these systems safe may mean containing the hazard behind guards or designing the machine so it won’t run until the operator is clear. Whether the danger is readily apparent, like moving parts, or invisible, like electrical current, the best safeguards make it impossible for the operator to even get near.”
- Rules: Workers should be on high alert for situations in which “[p]eople are bypassing the rules.Safety depends on people choosing to follow the rules…Even well-trained people can be lulled into a false sense of security and start taking shortcuts to make work faster or easier…If people are looking for ways around a safety system, it’s probably not well aligned with the operation. Rather than disabling the mechanism or retraining the operators, analyze the entire system and find a way to marry safety with the way the process really works.”
- Alarms: Workers need to notify management when “[a]larm systems don’t distinguish between emergencies and non-emergencies…if the system treats everything like an emergency, workers will treat nothing like an emergency. Frequent false alarms will lead workers to ignore the warning signs or circumvent them.”
- Obsolete: Workers must learn to keep an eye out for “[s]afety features [that] are outdated.A test of older fail-safes may find they no longer work — if they ever did in the first place…Maintaining a safe work environment means ongoing risk assessment. Safety professionals should perform regular audits of the equipment on the shop floor and keep an eye out for advancements that could make it safer.”
- Routine: Workers should alert management when they notice that “[s]afety features are not regularly tested and validated…the systems that keep workers safe should be checked on a regular basis.”
If workers can learn to recognize these five red flags, safety will become a higher priority and everyone in the workplace will benefit. As Thiel and Idzikowski acknowledge, “[t]he return on investment in safety is hard to measure. If a company invests millions in safety upgrades and there are no near-misses, was it a waste of money or did the upgrades do their job? A better question is what might realistically happen without safety upgrades.”
Safety Training: Begin with the Basics
Basic safety procedures are essential to keeping employees from becoming injured on the job. While manufacturing jobs can be dangerous, instituting safety procedures and ensuring that employees are properly trained are critical steps that employers must take to minimize the risk of injuries or death.
Not only does proper safety training reduce the number of workplace injuries, but it also adds to a company’s bottom line by improving productivity and reducing downtime caused by employees who can’t work when injured. But where should an employer start? How about at the beginning?
One of the most basic—and important—areas to focus on is the control of hazardous energy, often known by its more popular moniker “lockout/tagout.” According to the United States Department of Labor’s Occupational Safety and Health Administration (OSHA), “[e]nergy sources including electrical, mechanical, hydraulic, pneumatic, chemical, thermal, or other sources in machines and equipment can be hazardous to workers. During the servicing and maintenance of machines and equipment, the unexpected startup or release of stored energy can result in serious injury or death to workers.”
“Workers servicing or maintaining machines or equipment may be seriously injured or killed if hazardous energy is not properly controlled…Injuries may include electrocution, burns, crushing, cutting, lacerating, amputating, or fracturing body parts… Craft workers, electricians, machine operators, and laborers are among the millions of workers who service equipment routinely and face the greatest risk of injury.”
Fortunately, “[p]roper lockout/tagout (LOTO) practices and procedures safeguard workers from hazardous energy releases.” Teaching workers hands-on LOTO skills will help them to understand how to properly control hazardous energy and maintain a safe work environment.
DAC Worldwide Offers Superior LOTO Training
For companies looking to improve their safety training, a thorough review of current training materials is a great place to start. Do employees have access to hands-on training with actual components they’ll encounter on the job? If not, partnering with established companies to provide industrial-quality training systems that will stand the test of time will help ensure the continued safety of the workforce.
Employers don’t need to recreate the wheel to move toward a skills-based approach to hiring. DAC Worldwide, an industry-leading manufacturer of technical assessment and training tools, offers a variety of solutions to the problems employers face.
For example, DAC Worldwide offers a safety training system specifically designed to give employees the hands-on experience they need to master lockout/tagout skills. DAC Worldwide’s Lock-Out/Tag-Out Training System (811-000) features a realistic, simulated working process environment that facilitates introductory training with hands-on activities related to the process of identifying and locking out sources of dangerous potential energy in an industrial setting.
Since technical training is most effective when learners can gain hands-on practice with industry-standard components they’ll encounter on the job, the Lock-Out/Tag-Out Training System features a wide variety of common, industrial-quality components to provide learners with a realistic training experience that will build skills that translate easily to the workplace.
For example, the Lock-Out/Tag-Out Training System features:
- two PVC process tanks with removable covers, vents, drains, and process connections;
- PVC process network with block valves, 3-way valves, figure-8 blinds, and descriptive valve tags;
- fractional HP magnetic drive centrifugal pump;
- drain collection and distribution tubing network with valved central collection manifold;
- electrical controls, with provision for lock-out, including primary service disconnect, motor starter switch, in-line GFI protector, and system plug connection; and
- a comprehensive lock-out/tag-out tool kit with color-coded locks, tags, multi-lock hasps, specialty electrical locking devices, valve locking devices of multiple designs, and a dedicated toolbox.
The Lock-Out/Tag-Out Training System’s courseware consists of a training manual and hands-on exercises. These can be used as part of either an instructor-led course or self-directed study. A final performance assessment exercise is also provided, allowing the system to be used in an alternate configuration for testing purposes.
Contact a consultant with DAC Worldwide today to learn more about how their technical training tools can help you build the assessment and training program your company needs. Using DAC Worldwide training and assessment tools, you can transition to a skills-based hiring approach and fill the skills gaps in your organization!
- Published in News
Staying Protected: Hands-On Transformer Training in Safe, Controlled Environment
To view a multimedia presentation of “Staying Protected: Hands-On Transformer Training in Safe, Controlled Environment”, please click here.
The life of a power line worker can be a precarious one. From maintaining interstate power grids to servicing transmission lines and towers, line workers are often tasked with jobs that aren’t for the faint of heart.
The profession is considered one of the most dangerous in America, with 35 fatalities in 2019 around the United States. The compensation for such an intimidating trade, though, is notable.
According to salary.com, the average lineman salary in the United States is $80,026, as of February 2021. The career offers very realistic expectations of making upwards of $100,000 annually before turning 25 for younger students.
Today, the career is becoming safer, thanks to developing safety technologies. There are Linemen Training Schools all over the United States and Canada, with many finding interest in the unique field of high-voltage electrical technology.
Despite the demands, it is critical for workers to be properly trained on the power that electricity holds, both physically and metaphorically. Due to its hazardous nature, becoming a lineman requires extensive technical knowledge and safety skills to help ensure worker safety.
In the past, teaching the ins and outs of transformers was primarily paper-based, with some programs even opting for full-voltage training. Most of the time, the “real” learning was done on-the-job.
But things have changed in the electrical technology field. Training future lineworkers no longer requires a book-only approach, or the dangers that come with full voltages. DAC Worldwide’s Transformer Connections Training System (413-000) is a utility worker training aid that provides learners with real-world, hands-on practice working with transformers.
What is the Transformer Connections Training System?
DAC Worldwide’s Transformer Connections Training System is the ideal training tool for any lineman training program. It replicates the on-site conditions and circumstances that a utility worker encounters when making common transformer connections in the field. It allows the student to learn with a “hands-on” approach in a comfortable and controlled classroom environment.
Gone are the days of full-voltage training and paper-based learning, as the training unit is internally fused and includes a recalibrated reduced-voltage meter to make training safe, efficient, and realistic. As students train on the system at 4100 VAC, for example, they will only be operating at 41 Volts. This allows them to see real line voltage without the potential of getting hurt.
Put together in a welded steel cabinet, the Transformer Connections Training System is wired for both single-phase and three-phase activities. It includes 14 transformer cans, which are wired with different configurations to allow for a variety of set-ups, as well as a panel-mounted voltmeter and a phase rotation meter. It requires a 208 VAC / 3-phase / 60Hz / 4-wire connection.
In addition to the hands-on approach, the Transformer Connections Training System includes a Student Training Manual with a variety of topics, like performing single-phase transformer connections, identifying 3-phase connections, and demonstrating how capacitors affect line voltage and current. Learners will also learn how to demonstrate parallel single-phase and 3-phase transformers, and other transformer-related topics and skills.
Other Transformer Training Products
In addition to the Transformer Connections Training System, DAC Worldwide also offers slightly different variation called the Transformer Wiring Training System (408-000). This training tool is ideal for future industrial electrical programs and electricians, as it covers a basic course on transformers. It can also be used in residential electrical programs, as the system also shows how to connect a residential service.
Like the 418-000, the Transformer Wiring trainer takes the safe approach in learning by using low-voltage outputs while simultaneously simulating high-voltages. It replicates the single-phase transformer connections, as well as both delta-wye 3-phase transformer connections. All of the transformers are the same, and build into the unit, with the middle representing six different generators.
Students will be able to demonstrate proper installation of ground connections, primary and secondary side connections, and parallel transformer connections. The system also includes eight built-in instructor fault switches, which simulate failure conditions and allow real-time assessment and troubleshooting for students.
In addition to training systems, DAC Worldwide also offers two Transformers cutaways: one depicting a single-phase transformer, with the other showcasing a three-phase. Cutaways are real-world industrial components that have been restored, cut away, and refinished using durable urethane coatings. Each of these industrial components has been professionally sectioned to expose each device’s primary components, with functionality completely retained.
The Single-Phase Transformer (273-912) highlights a common shell-type, single-phase transformer found in manufacturing facilities and refineries, among others. The Three-Phase Transformer Cutaway (273-915) features a common coaxially-wound, three-phase, delta-wye transformer found in various industrial and commercial applications.
How Can DAC Worldwide Help Your Training Program?
With more than four decades of experience in industrial training, DAC Worldwide’s reach extends far beyond just electrical products. In fact, DAC Worldwide possesses knowledge and expertise in a wide range of technical topics, including Electronics, Fluid Power, Heat Transfer & Steam, HVAC, Machining & Measurement, Mechanical Drives, Oil Production, Process Control & Instrumentation, and Pumps, Compressors & Valves.
Our training aids range from training systems and sample boards, to models and dissectibles – with real-world, hands-on learning being the core of each product. For more information on how DAC Worldwide can enhance your industrial training program and provide you with the best training solutions available, please click here.
- Published in News
5 Skills Every HVAC Technician Should Possess
To view ‘5 Skills Every HVAC Technician Should Possess’ as a Multimedia Presentation, please click here.
While the national unemployment rate might be near all-time lows (3.5-percent in Dec. 2019), one industrial job is expected to grow by more than 46,000 jobs over the next decade: HVAC technicians.
Thanks to a push of commercial and residential building construction that is expected to drive employment growth and job opportunities, the employment outlook is expected to increase by 13-percent over the next 10 years. That is a sizable leap from the national average for all occupations, which sits at 5-percent over the next 10 years.
Not only are there currently enough jobs to go around, but a spike in upcoming retirements has some employers desperate for qualified talent. That’s good news for those interested in joining the HVAC field, as it places them firmly in the driver’s seat of finding an ideal professional match.
So with jobs aplenty, what skills are employers most focused on when hiring HVAC technicians? DAC Worldwide, a company with 40 years of experience working with industry and technical education, has compiled a list of the five most meaningful HVAC technician skills companies are in search of:
1. In-Depth Knowledge of HVAC Systems and Methods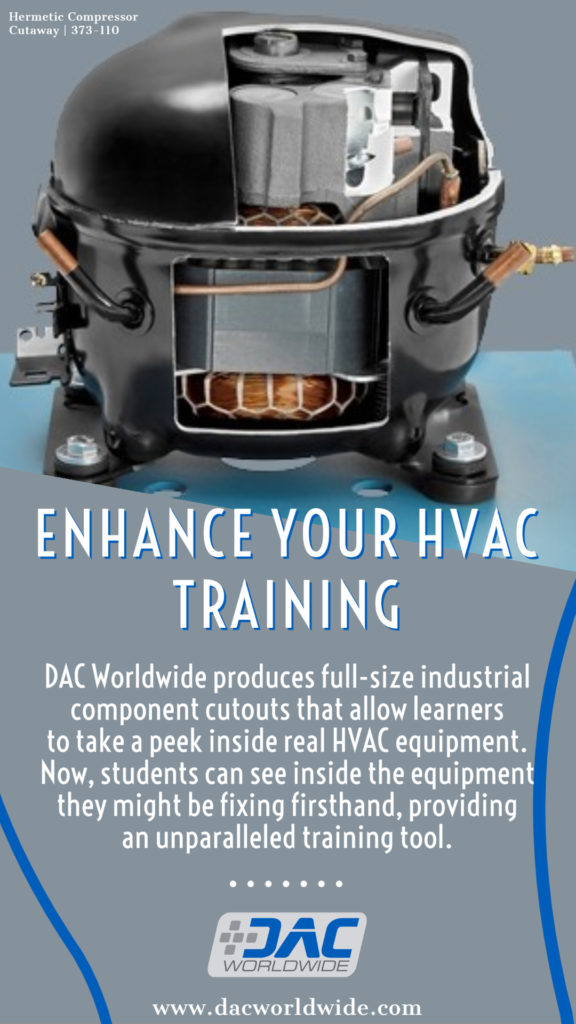
Doctors know medicine. Car mechanics know cars. To be successful in a profession, employees must understand the craft inside and out.
HVAC technicians are no different. They are responsible for knowing about a wide range of HVAC systems, controls, and installation methods, and quite literally, need to know about everything from hot to cold.
Whether technicians are threading and installing gas piping, or laying out duct systems, a deep understanding of all things HVAC is critical. Not only should technicians have the hands-on skills to perform each task, but they should back that up with a strong theoretical knowledge of their subject.
One way to enhance the understanding of HVAC systems is by taking a deep dive into how each piece of equipment works along the process. DAC Worldwide, for example, produces full-size industrial component cutouts that allow learners to take a peek inside real HVAC equipment for the first time. Now, students can see inside the equipment they might be fixing firsthand, providing an unparalleled training tool.
Today’s HVAC systems can be assembled, disassembled, repaired, and programmed, so having a background of mechanical skills is a key component to building a successful technician career. (After all, the more technical knowledge that a technician has from the start, the faster they can learn new skills, an attribute companies consider to be highly valuable.)
2. Acute Troubleshooting and Problem-Solving Skills
The goal for every HVAC technician is the same – aim for safe, timely, and effective services every time. In order for that to happen, techs need to be quick-thinking workers, equipped with a collection of problem-solving techniques, and possess familiarity with the latest diagnostic and testing equipment.
In just one work day, technicians may face a wide variety of issues: one customer may have total system failure, while another is dealing with noise issues, or temperature balancing problems. Being able to quickly size-up the problem, identify solutions, and implement a resolution is the key to finding success as an HVAC technician.
Problem-solving is impossible without an acute attention to detail. So along with ingenuity, employers are also looking for workers that are detail-oriented. Not only should technicians be able to track the work they are completing, but they should also be aware of the intricacies of the equipment they are working on. Sometimes, not paying attention to the details could be costly – either to the equipment, or the technician’s safety. Effective troubleshooting is a combination of accepted troubleshooting procedures supported by a solid knowledge of how these systems work to perform their operations.
Thanks to using real-world components, DAC Worldwide’s HVAC cutaways take detailed training to another level. By providing a look inside authentic components found in HVAC systems worldwide, learners can truly understand the fine details of the equipment’s inner workings. To truly understand how a component can fail, technicians must first understand how it works.
3. Extensive Knowledge of Safety Standards and Protocols
A day in the life of an HVAC technician is not exactly a walk in the park.
According to the U.S. Bureau of Labor Statistics, technicians have one of the highest rates of injuries and illnesses of all occupations. While most of these can be prevented by following safety protocols, it does have the potential to be a dangerous career.
So despite working heights, in confined spaces, or attached to scaffolding, having comprehensive knowledge of proper preventative safety standards can keep workers healthy and business moving. From hazardous tasks like lifting heavy objects to installing electric wires and controls, understanding personal protective equipment (PPE) and other safety codes could be the difference between technicians suffering an injury, or not.
On top of personal safety, HVAC technicians need to be well-versed in government regulations. The U.S. Environmental Protection Agency (EPA), for example, requires that all technicians who work with refrigerants be certified in proper refrigeration handling. There are additional regulations on how to handle pressurized gases, refrigerants, and other toxic or hazardous materials, so knowing regulations surrounding proper and safe disposal will not only protect technicians from an accident or injury, but will also keep clients and the environment safe.
4. Soft Skills, Communication, and Flexibility
Whether it’s a personal relationship or professional contact, we’ve all heard about the importance of first impressions: You only get one, so make it count.
Having a clean, professional appearance, listening to the customer, and showing all-around common courtesy are essential skills that can make or break a first meeting. Out in the field, employees are the face of the company, so making a good first impression is crucial for success of the business.
Possessing natural Customer Service skills are equally as important to this career as the technical skills a technician has. Not only is it a tech’s job to explain repairs and answer questions in a non-technical way, but they need to make the clients feel comfortable, building trust and rapport. This might require a little patience too, as their issues might have been ongoing, and frustration may be mounting. But in the end, having the ability to calmly and professionally talk through all of the issues and potential solutions will put everyone at ease.
Finally, in the world of an HVAC technician, every day is a new adventure. No matter the season, HVAC technicians are expected to work, even in uncomfortable situations.
Sometimes it’s too hot because the air conditioning isn’t working – other times the heat is out, making work conditions frigid. Even in the dead of winter, technicians might have to work outdoors, fixing heat exchanges, for example. Taking ‘flexible’ in a much more literal sense, some units are located in tight spaces, forcing technicians’ bodies to bend and curve in positions they didn’t know it could.
Being flexible is just part of the game. In this line of work, “That’s not my job” doesn’t exist. Sometimes, just being able to make changes on a whim, and occasionally just rolling with the punches, are the most effective tools a technician needs in his or her arsenal.
5. Willingness to Continue HVAC Learning and Training
If smart devices have taught us anything, it proves how quickly (and drastic) technology can change over decades. From minor tweaks to major overhauls, each update includes newer options and faster speeds.
The HVAC industry is no different. While it may not move with the veracity of cell phone technology, tools and equipment are being continuously adjusted to run more efficiently.
Today, there is also a continued push for greater energy efficiency, which includes phasing out hydrofluorocarbons (HFC) in favor of Global Warming Potential (GWP) refrigerants, and a rise of “zero emission building plans” and other green building standards. Soon, the HVAC industry will see an increase of variable speed technologies, which will improve electrical efficiency, air quality, and humidity control.
Without continued re-training within the field, technicians run the risk of encountering a component they can’t fix. So by having the willingness to continually hone their skills will not only be beneficial to their future professional success, but will also ensure timely, safe repairs and installations for all parties involved.
- Published in News