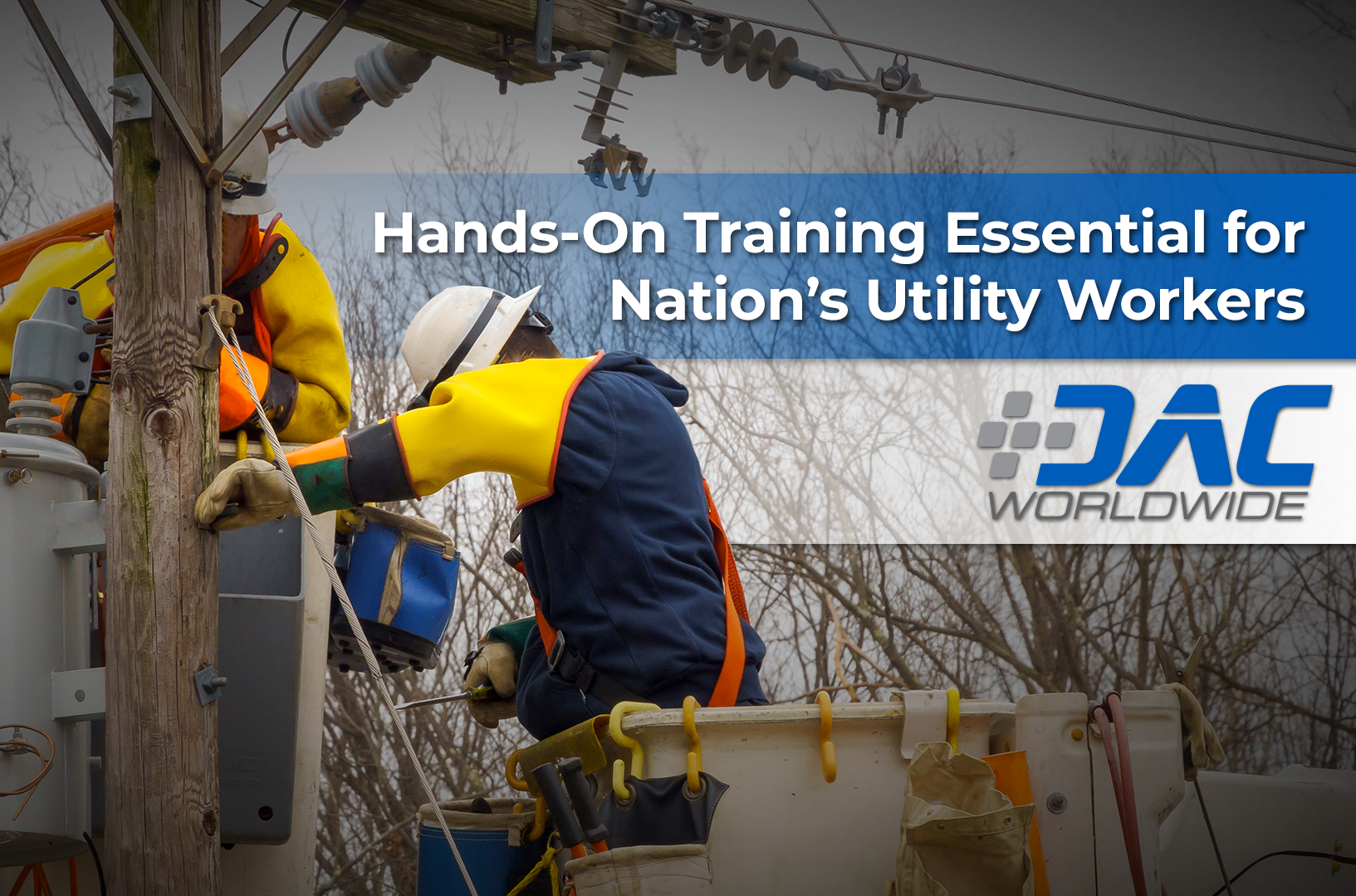
Click HERE to view Hands-On Training Essential for Nation’s Utility Workers as a multimedia presentation.
Do you ever daydream about going “off the grid”? For many, the thought of unplugging for an extended time away from life’s troubles sounds refreshing.
The reality underlying this common dream of escape is how thoroughly tied our lives are to the grid. What would our everyday routines be like without the utilities we so often take for granted?
We don’t give them much thought until Mother Nature intervenes with a foot of snow or an ice storm. When the lights go out, the Internet stops streaming, water freezes in the pipes, and furnaces quit heating, we think about nothing but our precious utilities until they return.
The unsung heroes in these situations are the nation’s frontline utility workers that must brave the elements to do their jobs in the worst circumstances. We wait anxiously and depend upon their expertise and dedication to restore our lives back to normal.
One day soon, though, we could find that wait lasting longer and longer. Why? Our nation’s utilities are facing an unprecedented — and worsening — shortage of workers with the skills necessary to keep the grid functional.
In this article, we’ll take a closer look at the looming shortage of utility workers across the country. We’ll also examine how one training center in Kansas is addressing the issue. Finally, we’ll discuss easy-to-use training options that any utility can use to provide safe, hands-on skills training to their frontline workers.
The Power & Utilities Skills Gap
Industries of all kinds across the nation are facing a critical shortage of skilled workers, and the power and utility industries are no exception. Demand for workers in these industries remains strong, but finding new workers to replace the many workers ready to retire is proving to be a substantial challenge.
In an Energy Central article, author Karen Marcus notes:
“As older workers retire, many utilities are finding it difficult to replace them, and to attract employees with the skills needed to advance a 21st century industry. According to T&D World, Airswift and Energy Jobline found in a survey of over 17,000 professionals that ‘48 percent of power professionals are concerned about an impending talent emergency, with 32 percent believing the crisis to have already hit the sector and 38 percent reporting that their company had been affected by skills shortages.’”
The shortage of skilled workers is real, and experts predict it’s only going to get worse in the future. According to Marcus:
“The U.S. Department of Energy (DoE) Quadrennial Energy Review (QER) reports that, according to one study, the industry will ‘need 105,000 new workers in the smart grid and electric utility industry by 2030, but expects that only 25,000 existing industry personnel are interested in filling those positions.’ The remaining 80,000 employees in this supply-demand mismatch will need to be filled through recruiting and training. However, the industry is not expected to meet the forecasted need with its current recruitment and training rates.”
Obviously, something needs to change. As the DoE QER states, “Industry hiring managers often report that lack of candidate training, experience, or technical skills are major reasons why replacement personnel can be challenging to find.”
If the power and utilities skills gap is to be bridged, utility companies must find a way to effectively provide safe, hands-on training to equip current and future workers with the critical skills they need to fill frontline positions as quickly as possible. Fortunately, solutions are available, and in the next section we’ll examine an exemplary approach taken by an association of municipal utilities in Kansas.
A Training Pioneer
Nearly two decades ago, Kansas Municipal Utilities (KMU), an association of more than 100 public utilities across the state of Kansas, recognized a dire need to effectively train the next generation of field workers. The groundbreaking solution KMU pioneered was finally brought to life a few years ago in the form of a $3.2 million training center.
As author Rick Aguilar notes in a T&D World article, KMU’s 20,000-square-foot training facility was seen as “a way to short-circuit the learning curve so utilities could swiftly prepare new hires to work as effective front-line employees.”
KMU’s training center allows for safe year-round training. Not only does the facility feature dozens of wood poles, but it also boasts a variety of industrial-grade components to create the most realistic distribution system possible.
For utility workers, real-world, hands-on training is essential. As Aguilar notes in his article:
“Because safety is an integral part of all utility work, the new training center helps the students learn through hands-on instruction. While they can pick up on key knowledge through sitting in class and reading books, the real rubber meets the road when they are actively participating in hands-on learning.”
For example, KMU’s training center allows workers “to get hands-on training in a controlled environment…[that] mitigates some of the hazards inherent in utility work, and it allows the field workers to make mistakes in a safe environment.”
KMU has found that a combination of classroom work and hands-on training is the ideal training experience. “For example, if KMU offers a workshop on transformer theory and connections, then the linemen can get hands-on experience immediately after they receive classroom instruction to connect their learning to actual work.”
Training Solutions for Everyone
As Aguilar notes in his article, “[m]any of the members of KMU are small in scope, and as such, they don’t have the ability to provide a comprehensive training program or build a facility of their own.” That’s why the KMU training center is such an important and valuable resource for Kansas utilities.
Nevertheless, “every utility needs to have a safe, qualified workforce.” So what are utilities in other states without the benefit of a KMU training facility supposed to do? Fortunately, there are a variety of training solutions that offer any utility the ability to provide critical hands-on skills training.
For example, DAC Worldwide manufactures a variety of unique training systems and industrial component cutaways that teach the essential hands-on skills frontline utility workers need most. In this final section, we’ll learn more about how utilities can use these systems to meet their training needs.
Transformer Wiring Training System (408-000)
DAC Worldwide’s Transformer Wiring Training System (408-000) is a realistic training device that replicates the conditions and circumstances that a utility worker encounters when making common power transformer connections in the field. This convenient tabletop training system provides hands-on training without the danger of full-voltage field experience.
For example, a 208VAC, three-phase source is stepped down, creating a 41VAC, three-phase system. The training system includes two complete sets of three-phase transformers so that paralleling can be explored. Users will also get first-hand experience using banana jacks, ground/primary connections, and secondary connections using both three-phase and single-phase applications.
Learners will study topics like analyzing transformer single-phase/three-phase voltages, identifying transformer turns ratio (TTR), and demonstrating how connections can produce incorrect motor rotation. They will also practice hands-on skills, such as performing transformer connections, interconnecting multiple transformers in Wye or Delta configurations, and simulating a burned-out transformer in a three-phase bank.
Transformer Connections Training System (491-000)
DAC Worldwide’s Transformer Connections Training System (491-000) teaches the key skills that a utility worker must master in order to confidently operate modern generating equipment, such as the paralleling of generators and connecting to a larger power grid. The system replicates the conditions and circumstances utility workers encounter when making common transformer connections in the field.
For example, learners can practice ground connections, primary connections, and secondary connections easily using banana jacks. Both three-phase and single-phase applications are provided, and a 208 VAC, 3-phase source is stepped down to a 41 VAC, 3-phase system for safety.
Users will find that the Transformer Connections Training System provides a safe and efficient, yet realistic alternative to a full-voltage field experience. Standard accessories include patch cords, fourteen (14) transformers, a panel-mounted voltmeter and phase rotation meter.
Industrial Transformer Cutaways
DAC Worldwide’s Single-Phase Transformer Cutaway (273-912) and Three-Phase Transformer Cutaway (273-915) are detailed, professionally-crafted transformer cutaways that depict a shell-type, single-phase transformer and a coaxially-wound, three-phase, delta-wye wired transformer, respectively.
Through careful sectioning, the complete internal configurations of these transformers can be seen. Details shown include the laminated steel core, primary and secondary windings, and primary insulation.
Common transformer brands and models are chosen for sectioning for industrial relevance. Users will gain valuable insight into the inner workings of these transformers that they will encounter on a regular basis in the field.