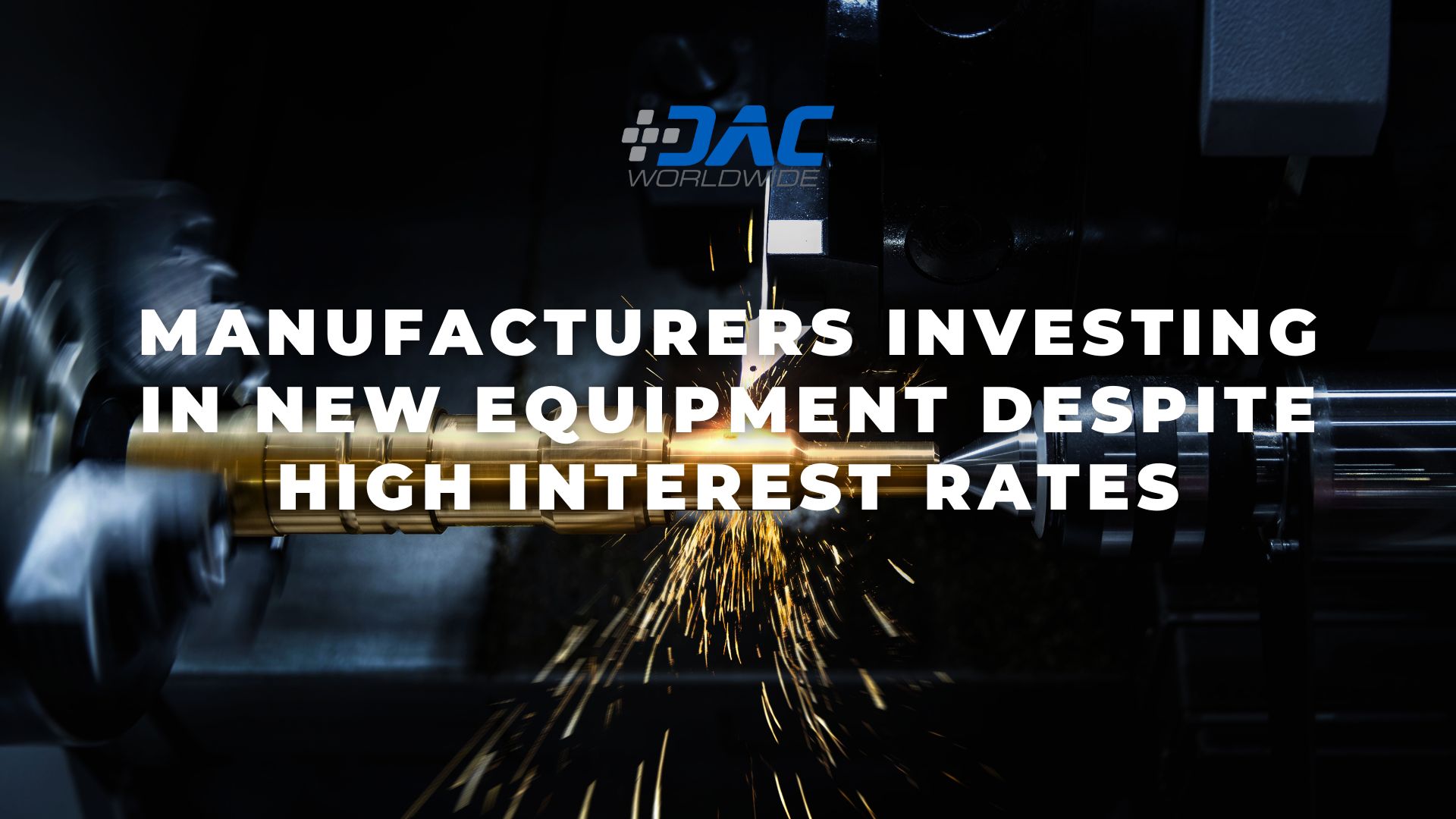
As consumers, it’s easy to see the effects of a prolonged battle with inflation. It seems like everywhere you go, it costs more these days for the things you need. From grocery stores and restaurants to gasoline and utilities, the consumer dollar just doesn’t stretch as far as it used to.
Are manufacturers experiencing something similar? If you watch the news, it’s pretty much been doom and gloom for some time now, even though many key economic indicators reflect a recovering economy that’s more robust than it’s been since the COVID-19 pandemic.
While it’s true that inflation and high interest rates can affect businesses just like they do consumers, there’s evidence that manufacturers see the light at the end of the tunnel. In fact, it appears that many manufacturers are ready to resume capital investment in the form of new manufacturing equipment orders.
A recent American Machinist article notes that “[a]n uptick in demand from machine shops and OEMs may indicate manufacturers are overlooking the high interest rates that have restrained new orders through the year to-date, recognizing sustained consumer and business demand for finished products.”
The article reports that “U.S. machine shops and other manufacturers increased their demand for capital equipment during May, with new metal-cutting and metal-forming and fabricating machines rising 21.8% from April to $386.7 million for the month. That represents a 6.5% increase in new orders from May 2023.”
“These figures are supplied by AMT – the [Association] for Manufacturing Technology in its U.S. Manufacturing Technology Orders report, a monthly review of new orders for machine tools (i.e., ‘manufacturing technology’), that serves as an indicator of future manufacturing activity because it quantifies machining operations’ investments in preparation for new production programs.”
In its report, AMT notes that these developments represent “a realization by manufacturers that capital investment is necessary ‘to meet the sustained demand for goods and machinery from consumers and businesses,’ in spite of the ongoing strain of high interest rates that have weighed against new-order activity since January.”
AMT also observed that “[d]emand for manufacturing technology among OEM is notably strong among electrical equipment manufacturers and power-generation and transmission equipment manufacturers. ‘These industries undoubtedly benefit from the government investment authorized by the CHIPS and Infrastructure acts and are therefore less sensitive to interest rates than others.’”
This is good news for electrical power generation and transmission equipment manufacturers. New equipment often means increased capacity, which in turn means new employees. Ensuring that new employees – and current employees – have the hands-on skills they need to succeed in the workplace remains a top priority.
How do companies and schools train the next generation of professionals with the electrical skills they need to succeed in the modern workplace? A thorough review of training systems is a great place to start. Do employees and students have access to hands-on training with actual components they’ll encounter on the job?
If not, partnering with established companies to provide industrial-quality training systems that will stand the test of time will help ensure a competent workforce. Be sure to check out DAC Worldwide’s variety of hands-on electrical training systems that feature the real-world components workers will encounter in the field!