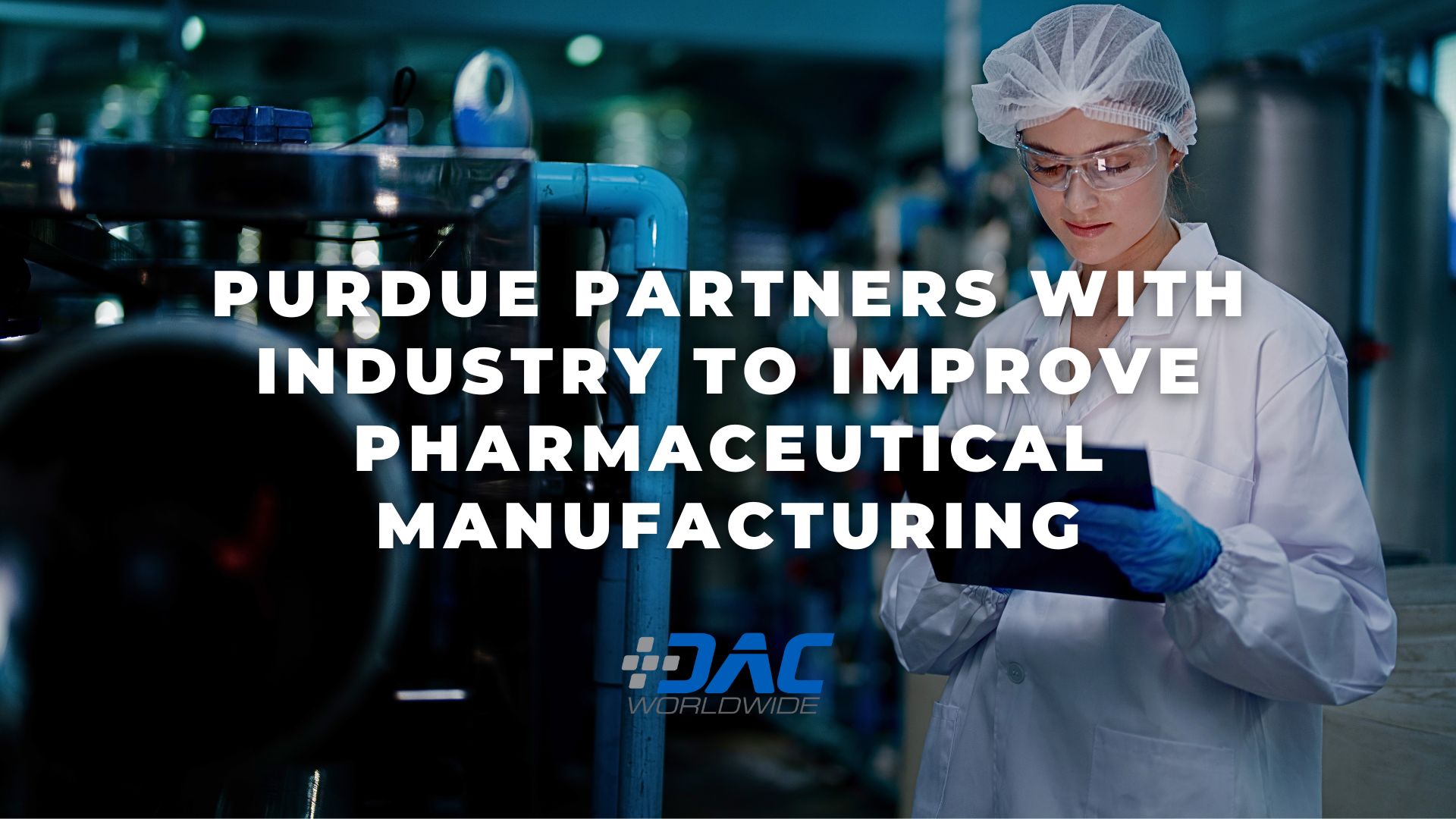
If the nation’s manufacturers ever hope to bridge the ongoing skills gap that prevents them from filling the hundreds of thousands of open manufacturing positions across the country, they’re going to have to get creative in terms of building partnerships with the educators preparing the next generation of workers.
Who else is better positioned to advise today’s educators about the skills workers need than the very companies that will be hiring students upon graduation? Yet, too few companies reach out to the educators in their area to build relationships with them and their students. Fortunately, some educational institutions are taking the lead in building the very important partnerships that will allow manufacturers to thrive for years to come.
For example, in a recent Contract Pharma article, author Kristin Brooks reports that “Purdue University, in collaboration with Eli Lilly and Co. and Merck & Co. Inc., launched the Young Institute Pharmaceutical Manufacturing Consortium, a collaborative effort to pioneer advances in pharmaceutical manufacturing.”
Brooks notes that “[o]perating within Purdue’s William D. and Sherry L. Young Institute for Advanced Manufacturing of Pharmaceuticals, consortium partners aim to revolutionize pharmaceutical manufacturing with a focus on sterile injectables and innovative aseptic manufacturing technology to ensure quality, safety and compliance.”
Karen Plaut, Purdue’s executive vice president for research, explains: “We’re on the frontier of Pharma 4.0 — autonomous experimentation, advanced robotics, big data, smart factories, AI and machine learning. Through this partnership, we will have a global impact in solving complex problems in the pharmaceutical and biopharmaceutical manufacturing ecosystem.”
Brooks points out that “[t]he consortium will rely on the research strengths of Purdue, Lilly and Merck, leveraging the organizations’ collaborative research relationship and workforce development programs…together with industrially relevant education and training for the next generation of scientific leaders and researchers.”
When it comes to training the next generation of advanced manufacturing workers, educators and industry partners alike would do well to partner with experts in technical training, such as DAC Worldwide. For example, consortium members could benefit from DAC Worldwide’s Smart Process Plant Training System (603-SP), a fully-functional, industrial-quality fluid process system that provides hands-on training in the measurement and control of five of the most common process variables: level, pressure, temperature, flow, and pH.
The system groups these process control elements into one complete piping system, which allows it to teach multiple configurations of flow loops, controls, and communications. The system incorporates both new and legacy technologies so that users are prepared for anything they might encounter on the job. These technologies work together to form a 3-level communication architecture:
- Device Level: Smart sensors monitor Level, Flow, Temperature, Pressure, and pH. They are connected via either IO-Link and Ethernet communication or HART communication.
- Control Level: A DCS and various PLCs and PIDs allow for operation and control of the system’s components.
- Enterprise Level: The DCS software provides Supervisory Control with data analytics for monitoring smart production, smart maintenance, etc.
The Smart Process Plant uses a Distributed Control System (DCS) that features Supervisory Control software. This software is Rockwell Automation’s PlantPAx, and it acts as the backbone of the system. It gathers and organizes data and creates dashboards that represent the real-time status of the processes being carried out by the system.
The Smart Process Plant Training System features a wide variety of common, industrial-quality components and instruments to provide learners with a realistic training experience that will build skills that translate easily to the workplace. The Smart Process Plant also includes multiple experiments, which simulate both continuous and batch process control loops that are widely used in many process industries. These experiments include:
- Basic and Advanced Bioreactor Applications
- Clean-In-Place (CIP) Skid Application
- Boiler Drum Level Application
- Wastewater Treatment Application
With these experiments, learners will explore a wide variety of fundamental process control topics, including: temperature, level, flow, pressure, and pH ratio control; agitation; sequence control; continuous control; 3-element control; feed forward/cascade control; and pump lead/lag demand. The Smart Process Plant Training System is only one of DAC Worldwide’s many process control and instrumentation training systems. Visit DAC Worldwide online to learn more about its many other training systems, as well as advanced chemical engineering training systems from its partner, Pignat SAS!