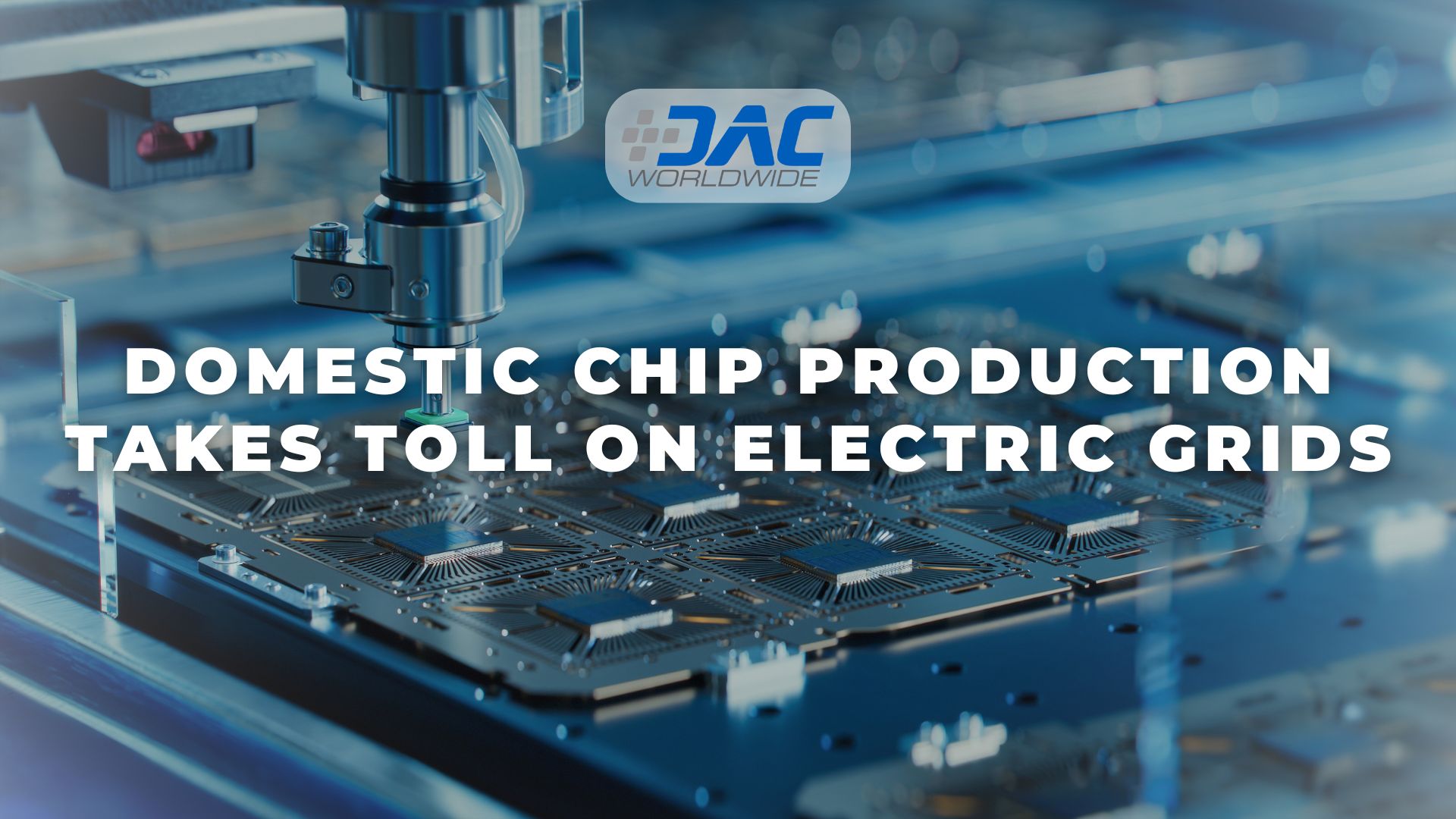
Do you remember the good old days of the COVID-19 pandemic? Me neither. Empty store shelves devoid of your favorite products. Supply chain disruptions affecting every aspect of your modern life. No, those were not fun times.
Anyone shopping for a new or used vehicle during the pandemic probably remembers the lack of vehicle supply leading to huge price increases. In some cases, thousands of new vehicles sat in parking lots waiting for one tiny, but critical component—usually a semiconductor or “computer chip”—before they could be shipped to dealers for sale.
The fact that our auto industry relied almost exclusively on foreign suppliers for such key components did not go unnoticed by the federal government. In a recent IndustryWeek article, author Sarah Shinton notes that “[i]n 2022, the White House signed the CHIPS and Science Act into law, a bipartisan effort to increase domestic advanced semiconductor manufacturing. The legislation made a historic $52 billion investment in American semiconductor research, manufacturing and workforce development.”
Is your area one of those lucky enough to have acquired a new semiconductor manufacturing facility? If so, you may not have heard a lot about it yet. Shinton points out that “new projects are facing construction delays and permitting issues.”
More problematic, however, is the fact that there’s a larger issue looming: “the country might be unable to generate enough electricity to power new fabrication plants, leaving billions of dollars in federal funds stranded and one of its most critical supply chains vulnerable.”
Shinton notes that “[w]hile manufacturing semiconductors has always been energy-intensive, the process is becoming even more so as chips are developed to be smaller and more powerful. The most advanced semiconductors require extreme ultraviolet (EUV) lithography machines, which use ultraviolet light produced by rapid-fired lasers to burn fine details on silicon wafers.”
Unfortunately, “these machines consume 10 times as much power as earlier generations of equipment.” How much power is that? A lot. Shinton points out that “the Taiwan Semiconductor Manufacturing Company (TSMC), the world’s leading semiconductor manufacturer,…now consumes more electricity than some U.S. states.”
This presents a huge problem for future chip fabrication plants in the U.S. According to Shinton, “semiconductor manufacturing creates large pockets of demand in the areas where fabrication plants are located. A rapid increase in load presents challenges for grid operators who maintain the delicate balance between electricity supply and demand, preventing curtailments or worse, blackouts.”
The phasing out of coal-fired power plants in favor of alternative sources, such as natural gas, solar, and wind, could also be problematic. “The vast amount of electricity needed to onshore this new manufacturing comes at a time when America’s power grid is increasingly unreliable as the country undergoes rapid changes…many regulators are raising alarms that power plants are being retired faster than they are replaced, leaving the country at risk of electricity shortages.”
Moreover, “[t]hese mass retirements are also happening while electricity demand nationwide is increasing from data center growth, expansions in manufacturing and intensifying weather conditions…Over the past year, the five-year load growth forecast nearly doubled, jumping from 2.6% to 4.7%…Without expanding the high-capacity transmission system, our grid will struggle to meet this demand.”
What do these problems mean for the future workforce? Not only will dozens of semiconductor manufacturing facilities need highly skilled workers for their plants, but the industries supporting these new ventures will need thousands of workers with fundamental electrical skills as public utilities work together with industry to ensure a stable electrical grid for the future.
How do companies and schools train the next generation of professionals with the electrical skills they need to succeed in the modern workplace? A thorough review of training systems is a great place to start. Do employees and students have access to hands-on training with actual components they’ll encounter on the job?
If not, partnering with established companies to provide industrial-quality training systems that will stand the test of time will help ensure a competent workforce. Be sure to check out DAC Worldwide’s variety of hands-on electrical training systems that feature the real-world components workers will encounter in the field!