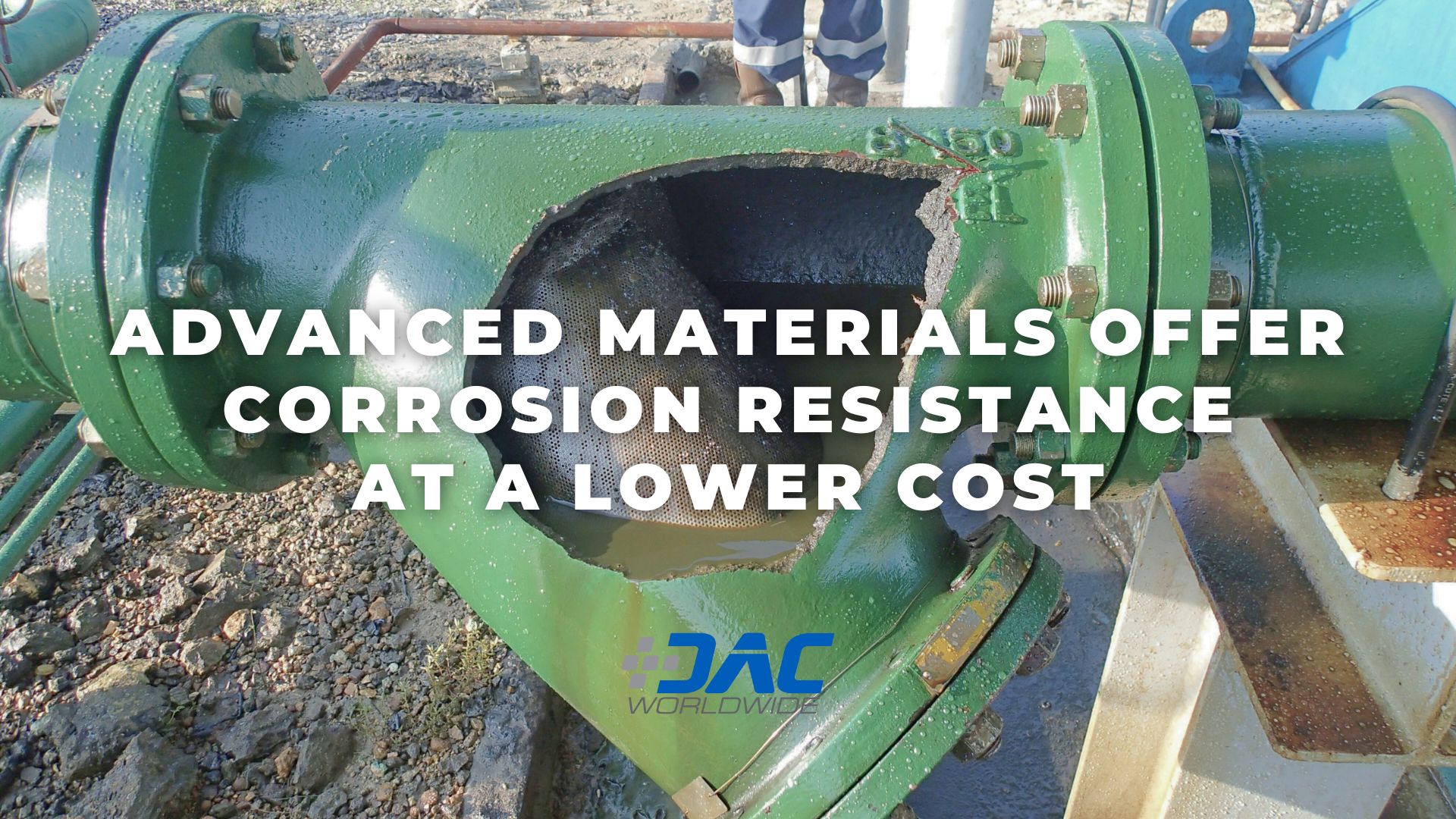
Industrial strainers play a critical role in a wide variety of process control applications. According to a recent New Equipment Digest article by Del Williams, “from desalination, wastewater treatment, and irrigation to power generation and the production of food, pharmaceuticals, consumer, and industrial products,” “[i]ndustrial strainers are essential for screening out debris and large particulates to protect crucial downstream equipment and processes.”
For many applications, strainers constructed of standard carbon steel are perfectly fine. However, experts note that “corrosive environments such as those involving seawater, erosive slurries, or aggressive chemicals can quickly corrode conventional equipment. This can lead to potential issues in safety, quality, and compliance as well as production downtime, requiring premature strainer component replacement.”
For these harsh environments, “duplex or super duplex stainless-steel construction is used to resist corrosion, but at considerable cost.” That’s why many industries have been searching for “a more economic, durable alternative,” and they may have found it in fiber-reinforced plastic (FRP).
Robert Presser, Vice President of Acme Engineering Prod., Inc., a North American manufacturer of industrial self-cleaning strainers, claims that “[t]oday, a much more cost-effective option is to use Fiber-Reinforced Plastic (FRP) strainers that are specifically designed to be resistant to corrosive environments at a fraction of the cost of duplex or super duplex stainless steels.”
So what exactly is FRP? According to Williams, “FRP is a composite material made up of polymer and supported with fibers for added strength. FRP is already widely used for applications such as the power plant piping used to carry seawater for once-through process cooling.”
Williams notes that “[w]ithin industrial markets, OEMs are now using FRP in various applications where superior corrosion resistance is required at lower cost…Industries can save approximately half the cost or more when the strainer’s intake vessels and piping are built with FRP, and only the internals are constructed with super duplex.”
Regardless of what materials they’re made of, industrial strainers remain an important piece of many different types of process applications. Maintenance technicians must be familiar with different types of strainers, including how to keep them operating at peak efficiency.
That’s why DAC Worldwide offers several training tools designed to help industrial maintenance technicians become familiar with industrial strainers:
- DAC Worldwide’s Dual Basket Straining System Cutaway (273-330) is a realistic sectioned example of a duplex basket strainer commonly found in petro-chemical plants, refineries, and other similar industrial environments. Often used in process applications where significant debris is encountered, these easily-maintained devices dependably protect downstream equipment, such as centrifugal pumps, meters, valves, and spray nozzles from damage.
- DAC Worldwide’s Single Basket Straining System Cutaway (273-320) is a realistic sectioned example of a simplex basket strainer.
- DAC Worldwide’s Y-Type Straining System Cutaway (273-310) is a realistic, sectioned example of a y-type strainer. It supports training relating to industrial, commercial, and domestic process systems. Y-type strainers mechanically remove solids from flowing liquids and gases by incorporating a removable wire mesh or perforated straining element. Capable of withstanding significant pressures, the device is commonly used to protect heat exchangers, pumps, valves, and other valuable process equipment.
Be sure to check out DAC Worldwide’s other Process Control and Instrumentation training tools and contact a DAC Worldwide representative to learn how you can improve your training today!