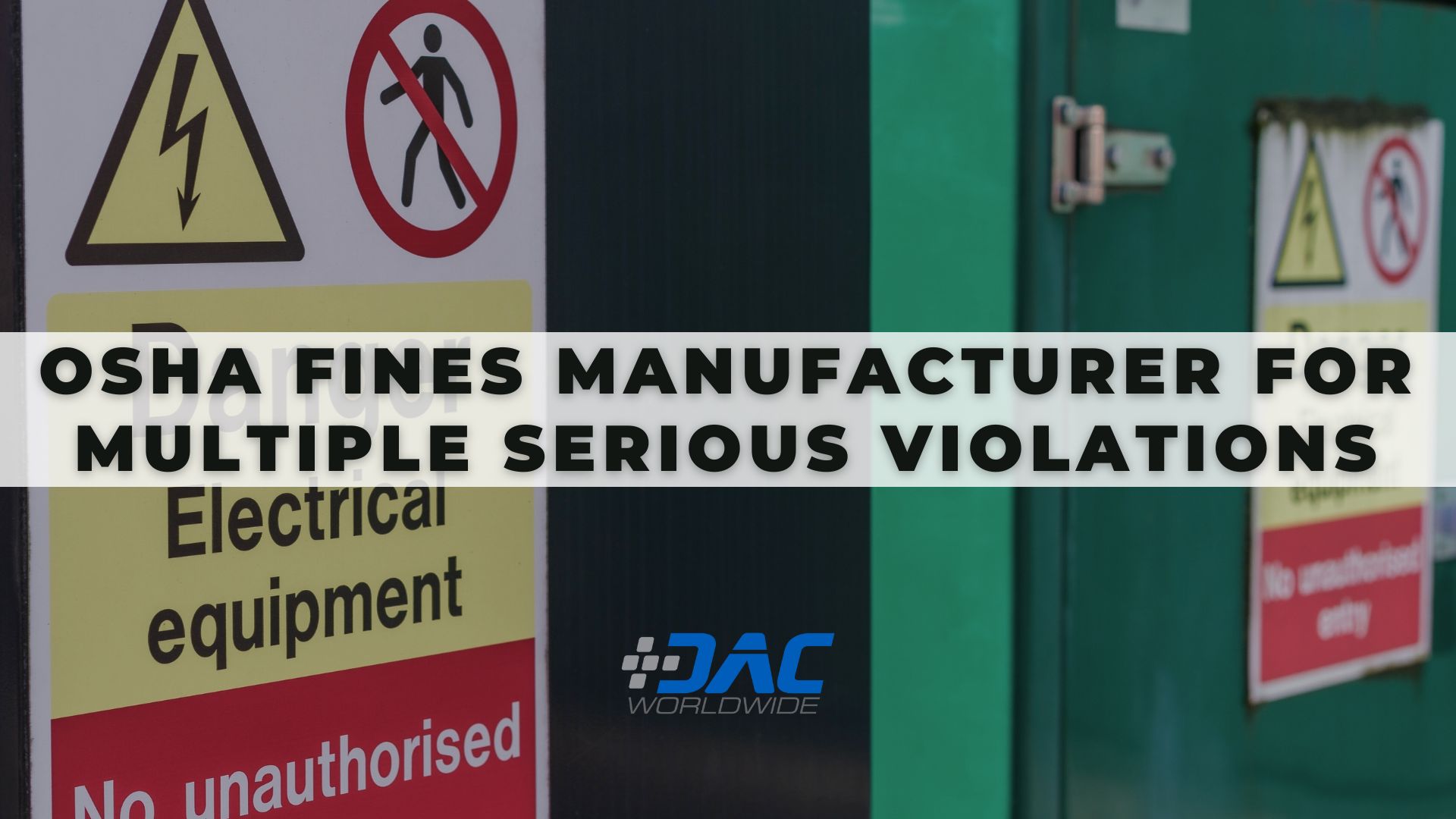
Did you hear the latest parental advice on how to keep kids from chewing on electrical cords? You ground them until they conduct themselves properly!
OK, we may have started this article with a (terrible, absolutely awful) joke, but we did so to make a point: electrical safety is no joke, especially in the workplace. In fact, bad dad jokes are the only time electrical safety is a laughing matter.
That’s a lesson that a plastic and resin manufacturer with facilities in Georgia and Alabama learned the hard way recently. According to a recent Plant Services article by Alexis Gajewski, “[a]n [Occupational Safety and Health Administration] OSHA investigation has determined that Crown USA Inc. could have prevented the death of a 37-year-old maintenance technician…if they were following required safety rules designed to keep machines from starting up during maintenance.”
Gajewski notes that “[t]he worker was inside an unlocked hooding palletizer, servicing the machine, when they suffered fatal crushing injuries.” OSHA Area Director Jeffery Stawowy said, “Employers must understand federal workplace safety regulations exist to help prevent tragedies like the one that occurred at Crown USA Inc.”
The resulting OSHA investigation revealed “eight serious and six other-than-serious violations. These violations include failing to implement adequate machine guarding, a lack of training on energy control procedures, exposing workers to serious respiratory hazards, and failing to provide proper personal protective equipment (PPE).”
Not only did a maintenance worker needlessly lose their life, but the company also “faces $98,699 in penalties.” Other companies would be wise to learn from Crown USA Inc.’s shortcomings and institute rigorous safety training, including adequate training on energy control procedures.
Manufacturers can always benefit from a regular audit of safety training. The best way to improve a workplace’s safety culture and teach workers to prioritize safety is to implement a quality safety program that teachers workers the knowledge and skills they need to stay safe in the workplace.
As previously mentioned, one of the most basic—and important—areas to focus on is the control of hazardous energy, often known by its more popular moniker “lock-out/tag-out or LOTO.” According to OSHA, “[e]nergy sources including electrical, mechanical, hydraulic, pneumatic, chemical, thermal, or other sources in machines and equipment can be hazardous to workers. During the servicing and maintenance of machines and equipment, the unexpected startup or release of stored energy can result in serious injury or death to workers.”
That’s exactly the lesson that Crown USA Inc. learned too late. Fortunately, “[p]roper lock-out/tag-out practices and procedures safeguard workers from hazardous energy releases.” Teaching workers hands-on LOTO skills will help them to understand how to properly control hazardous energy and maintain a safe work environment.
For companies looking to improve their safety training, partnering with established companies to provide industrial-quality training systems that will stand the test of time will help ensure the continued safety of the workforce.
For example, DAC Worldwide offers a safety training system specifically designed to give employees the hands-on experience they need to master lock-out/tag-out skills. Be sure to check out DAC Worldwide’s Lock-Out/Tag-Out Training System and contact a DAC Worldwide representative to learn how you can improve your training today!